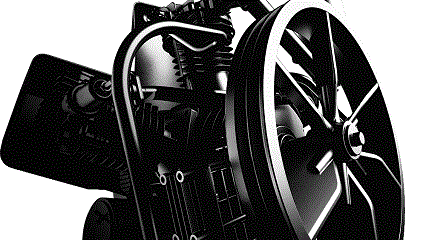
Choosing the right air compressor is essential for ensuring efficiency and effectiveness in various applications. Here are key factors to consider when selecting a compressor:
1. Airflow and Pressure Requirements
Understanding the airflow (measured in cubic feet per minute, CFM) and pressure (measured in pounds per square inch, PSI) requirements of your tools is crucial. Each tool has specific CFM and PSI needs, which dictate the compressor’s capability to perform tasks effectively. For example, a nail gun may require less airflow than a spray painter, necessitating careful evaluation of all tools used[1][3].
2. Duty Cycle
The duty cycle indicates how long a compressor can run continuously without overheating. If your tools are used intermittently for short periods, a reciprocating compressor may suffice. However, for continuous operation exceeding eight hours a day, a rotary screw compressor is more suitable due to its ability to handle prolonged use without damage[3][8].
3. Future Expansion
Consider potential future needs when selecting a compressor. It’s wise to choose a model that can accommodate additional tools or increased usage over time. This foresight helps avoid the need for an early upgrade[1].
4. Air Quality
Depending on your application, you may require specific air quality standards. For instance, industries like food processing may need oil-free compressors, while others might prefer oil-lubricated models for better performance and longevity[1][4].
5. Portability and Power Source
Decide whether you need a portable or stationary compressor based on your workspace requirements. Additionally, assess the available power sources—gas or electric—and ensure compatibility with your operational setup[5].
6. Noise Levels
In environments where noise is a concern, consider compressors designed for quieter operation. This is especially important in residential or commercial settings where excessive noise could be disruptive[1][4].
By evaluating these factors—airflow and pressure requirements, duty cycle, future expansion needs, air quality standards, portability, power source options, and noise levels—you can make an informed decision that best fits your specific air compression needs.